Carreaux de ciment : comment sont-ils fabriqués ?
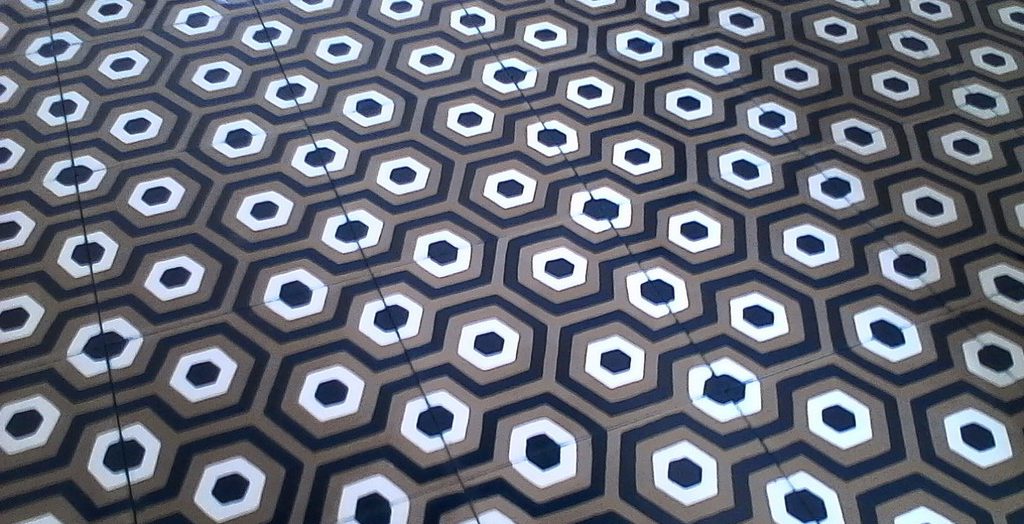
La méthode de fabrication des carreaux de ciment a été inventée à la fin du XIXe siècle. Le procédé n’a subi aucun changement au fil des siècles. La production de ce type de carreau s’effectue de manière artisanale. L’ensemble des accessoires et des outils qui interviennent dans le processus de fabrication sont de fidèles répliques de ceux qui ont été employés à l’époque. Toutefois, le procédé requiert une grande précision, de l’outillage et une justesse des dosages. De ce fait, il est extrêmement technique et chaque carreau fabriqué à la main constitue une pièce unique. Voici les différentes étapes de la fabrication de carreaux en ciment.
Étape 1 : Nettoyage du moule et mise en place du séparateur
Le moule utilisé pour la fabrication d’un carreau en ciment est en acier. Pesant 15kg, il est composé d’un cadre, d’un fond et d’un tampon. Avant chaque moulage, il est soigneusement nettoyé à l’aide d’un racloir et d’une brosse. Le fond de moule est ensuite graissé et lustré pour faciliter le démoulage.
Un diviseur en laiton est placé sur le fond du moule. Il est doté de cloisons verticales qui forment des alvéoles. Les différentes couleurs du carreau en ciment sont coulées dans ces compartiments. Cette pièce fait l’objet de contrôles fréquents et elle est régulièrement passée au marbre pour assurer sa planéité et son adhérence au fond du moule. Un défaut d’étanchéité peut, en effet, engendrer la « fuite » d’une couleur vers une autre alvéole et altérer les traits du motif.
Étape 2 : la couche de surface et le retrait du séparateur
Pour couler le mortier de couleur constituant la couche de surface dans les diviseurs, il faut utiliser un biberon ou une louche. Après, le moule est secoué pour assurer une répartition uniforme du mortier dans le séparateur.
Le mortier fin gâché employé se compose de ciment blanc mélangé avec de la poudre de marbre blanc teintée à l’aide d’oxydes métalliques dont les couleurs se déclinent en une palette d’environ 80 coloris. La couche de couleur est très liquide. Elle s’étale sur quelques millimètres au fond du moule. Le motif du carreau en ciment est réalisé dans la masse, sur une épaisseur de plusieurs millimètres. Le temps et la difficulté d’élaboration du carreau augmentent au fur et à mesure de la multiplication de couleurs et d’alvéoles.
Lorsque les couleurs sont versées, le séparateur est retiré doucement. Au cours du retrait des cloisons, les pattes de couleurs se mélangent entre elles. Toutefois, la couche qui est déposée au fond du moule, celle qui forme la surface du carreau, reste stable. Pour cristalliser la couche de mortier liquide, elle est immédiatement saupoudrée d’un mélange de sable et de ciment sec.
Étape 3 : remplissage du moule avec du mortier gris et le passage à la presse
La 3e étape consiste à remplir le moule avec un mortier grossier composé de ciment gris et de sable. Lorsque le cadre est plein, le moule est fermé. Un motif en relief est imprimé à l’aide d’un tampon pour indiquer sur la face cachée du carreau en ciment la marque du fabricant.
Chaque cadre est doté d’une charnière (à l’extrémité d’une de ses diagonales) et d’un système de réglage pour une fermeture rapide et pour faciliter l’introduction et l’extraction du produit.
S’ensuit la phase de passage à la presse. L’excès d’eau qui s’est immiscée dans la couche colorée s’intègre dans la couche de structure. La teneur en eau et la plasticité de toutes les couches deviennent ainsi homogènes.
Étape 4 : l’extraction du moule et le trempage
La phase d’extraction commence par le retrait du tampon, le déverrouillage et le retrait du cadre. Le carreau est par la suite délicatement démoulé. Cette étape requiert une maîtrise de la technique d’extraction, car le carreau ne constitue encore qu’un agglomérat de ciment n’ayant aucune résistance. Le produit obtenu est ensuite entreposé sur une base bien nivelée et laissé au repos pendant 24 heures avant de passer à l’étape de trempage.
Cette phase est extrêmement délicate. En raison des nombreuses manipulations à effectuer pendant l’extraction, il est quasiment impossible d’automatiser la fabrication de carreaux en ciment. C’est ce qui explique le fait que le processus de fabrication de ce type de revêtement est resté au stade artisanal et réalisé à la main.
Les carreaux sont ensuite transportés dans un local où ils sont trempés dans de grands bacs d’eau pour hydrater l’agglomérat de ciment et assurer sa prise pour donner, au final, une parfaite fragmentation.
Étape 5 : le séchage
Les carreaux de ciment sont entreposés sur des étagères où ils sécheront pendant une période allant de 3 à 4 semaines. Enfin, ils sont conditionnés pour être livrés à leur destinataire final, soit un distributeur, soit une entreprise de construction ayant passé une commande spécifique.
Pour garantir la qualité des carreaux de ciment, les artisans utilisent des matériaux spécialement sélectionnés, conformes aux normes en vigueur (norme BENOR)